Why Food Suppliers Lose Money on Inventory & How to Fix It
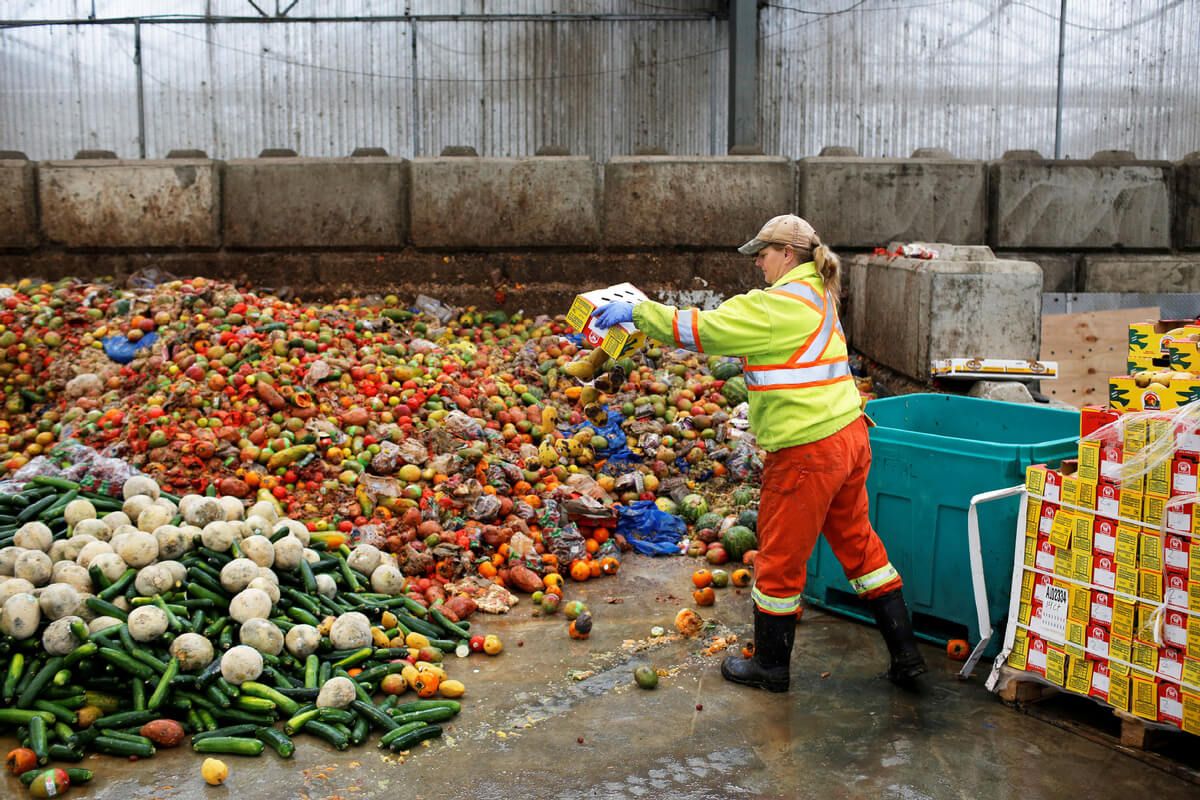
1. Poor Inventory Management
Ineffective inventory tracking leads to spoilage, stock discrepancies, and inefficiencies. Inaccurate records result in either overstocking, causing waste, or understocking, leading to missed sales. Manual tracking methods further increase the likelihood of human error, making inventory control more challenging. Poor inventory visibility also makes it difficult to make informed purchasing decisions, leading to reactive rather than proactive inventory management.
Solution: Implementing cloud-based, automated inventory tracking software eliminates human error, ensures real-time stock visibility, and optimises reordering processes. These systems help reduce spoilage by providing accurate expiration date monitoring and facilitating demand-driven restocking. Additionally, integrating barcode or RFID scanning can improve inventory accuracy and reduce misplaced stock.
2. Perishability of Food Products
Food suppliers deal with highly perishable items like fresh produce, dairy, and meat. Without precise demand forecasting, excess stock can spoil before it is sold, while insufficient stock results in missed revenue opportunities. Inconsistent storage conditions, such as fluctuating temperatures, further shorten shelf life and lead to avoidable waste. Mishandling during transportation and improper packaging can also contribute to spoilage before products reach the customer.
Solution: Utilising IoT sensors and automated temperature monitoring ensures optimal storage conditions, reducing spoilage risks. Implementing First-In, First-Out (FIFO) inventory rotation minimises waste by ensuring older stock is used first. Suppliers should also invest in high-quality packaging and transportation solutions that maintain food integrity during transit.
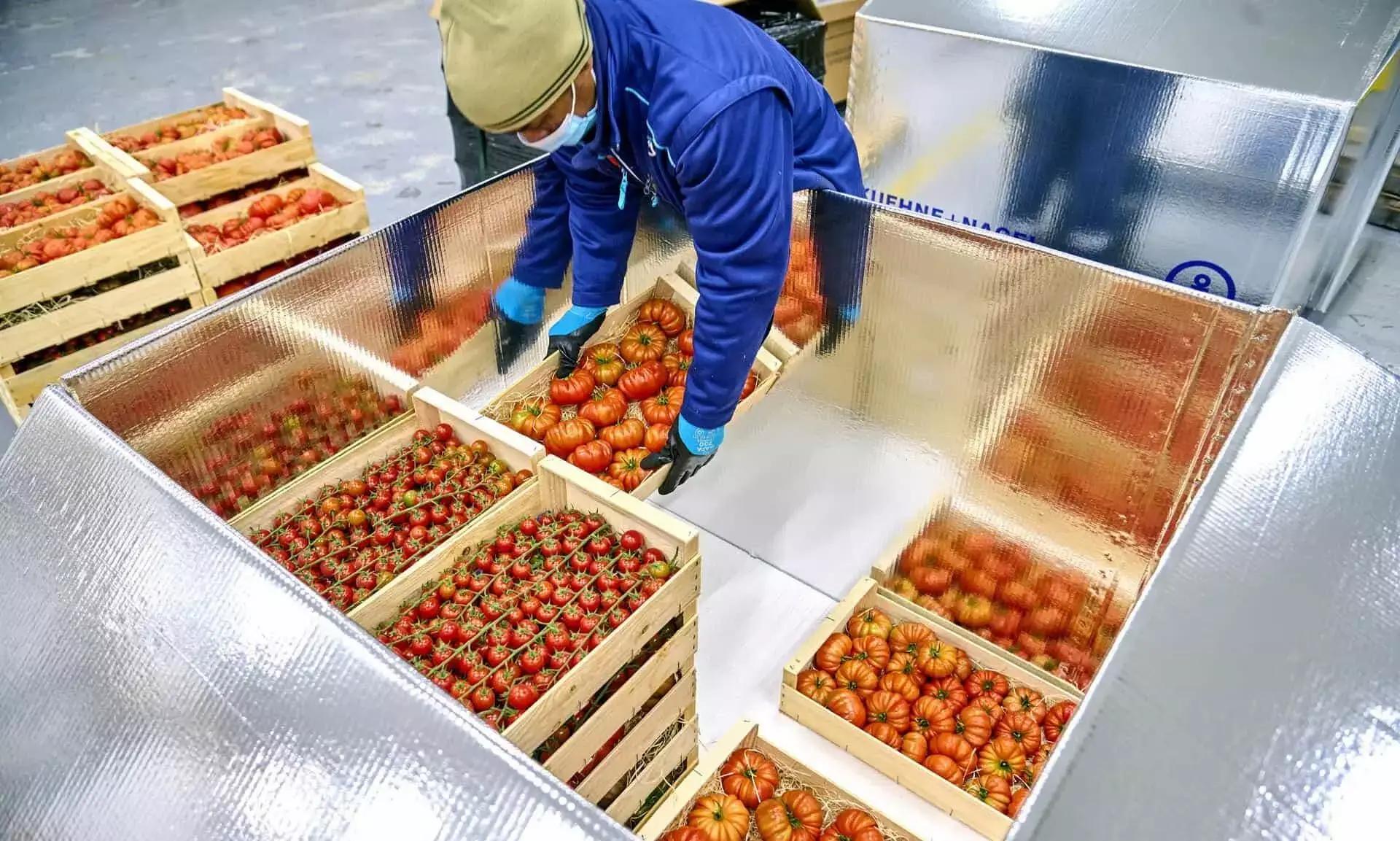
Start optimising your inventory today with these best practices.
3. Forecasting Errors
Predicting demand inaccurately leads to significant losses. Overestimating sales results in surplus goods that expire before being sold, while underestimating demand causes stock shortages, leading to lost customers and rushed, costly replenishments. Factors contributing to poor forecasting include unreliable historical data, seasonality miscalculations, and the absence of advanced data analytics. Without accurate forecasting, suppliers may struggle with fluctuating demand trends and seasonal peaks.
Solution: Leveraging AI-driven forecasting tools helps suppliers accurately predict demand patterns, reducing excess inventory and stockouts. Advanced analytics incorporate real-time data, historical trends, and market conditions to enhance forecasting accuracy. Collaborating with retailers and distributors to share sales data can also improve forecasting precision and alignment with market trends.
4. Inefficient Storage Practices
Poor warehouse organisation increases the risk of misplaced or expired stock. Lack of proper shelving, insufficient temperature control, and inconsistent labeling create inefficiencies, leading to unnecessary reorders and financial losses. Overstocked storage areas may also encourage pest infestations and product contamination. Additionally, a lack of defined storage zones can make it difficult for employees to locate and retrieve stock efficiently, causing delays in order fulfillment.
Solution: Enhancing warehouse organisation through proper shelving, temperature control, and clear labeling improves efficiency. Regular inventory audits help identify discrepancies before they escalate, while optimising storage layout can improve inventory visibility and turnover. Implementing automated warehouse management systems (WMS) can further streamline operations, ensuring products are stored and retrieved efficiently.
Find the Best Inventory Management Systems for Wholesale Food Suppliers
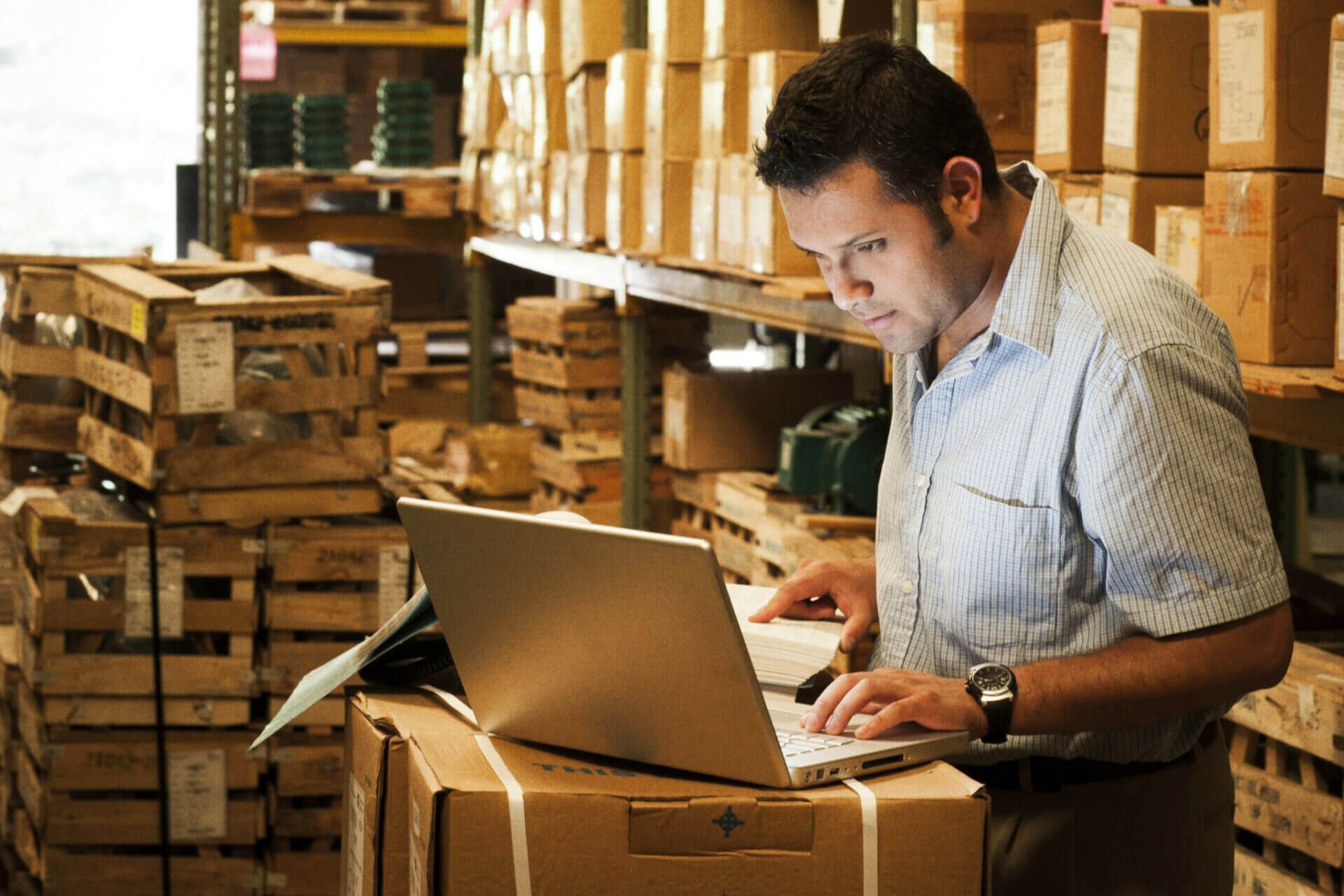
5. Supply Chain Disruptions
External factors such as weather events, labor shortages, and transportation delays disrupt inventory replenishment. This leads to stock shortages, forcing emergency restocking at higher costs, or excessive stockpiling, which increases waste and storage expenses. Additionally, fluctuating input costs during supply chain disruptions further strain profit margins. A lack of supplier diversification can make food suppliers more vulnerable to unexpected shortages.
Solution: Strengthening supplier relationships and maintaining a flexible restocking strategy ensures better supply chain resilience. Sharing inventory data with suppliers improves responsiveness, while diversifying supply sources minimises disruption risks. Establishing contingency plans, such as backup suppliers and alternative transportation routes, can mitigate the impact of supply chain disruptions.
6. Outdated Technology and Manual Processes
Many food suppliers still rely on outdated inventory systems that lack real-time tracking, automation, and data integration. This results in inaccuracies, inefficiencies, and slow response times when adjusting stock levels. Without predictive analytics or cloud-based inventory management, suppliers struggle to optimise their inventory strategy. Additionally, reliance on paper-based systems or spreadsheets increases the risk of human error and miscommunication.
Solution: Upgrading to modern inventory management systems with real-time tracking, automation, and predictive analytics enhances efficiency and accuracy. Cloud-based platforms improve accessibility and integration across supply chain operations. Implementing mobile-friendly inventory solutions enables employees to update stock records in real time, improving accuracy and efficiency.
Open Pantry offers a cloud-based, automated inventory management system designed specifically for food suppliers. With real-time tracking, predictive analytics, and seamless integration, Open Pantry eliminates the inefficiencies of outdated systems. Its mobile-friendly platform allows employees to update stock records on the go, reducing errors and improving inventory accuracy. By utilising AI-driven forecasting and automated stock replenishment, Open Pantry helps suppliers optimise inventory levels, minimise waste, and enhance overall operational efficiency.
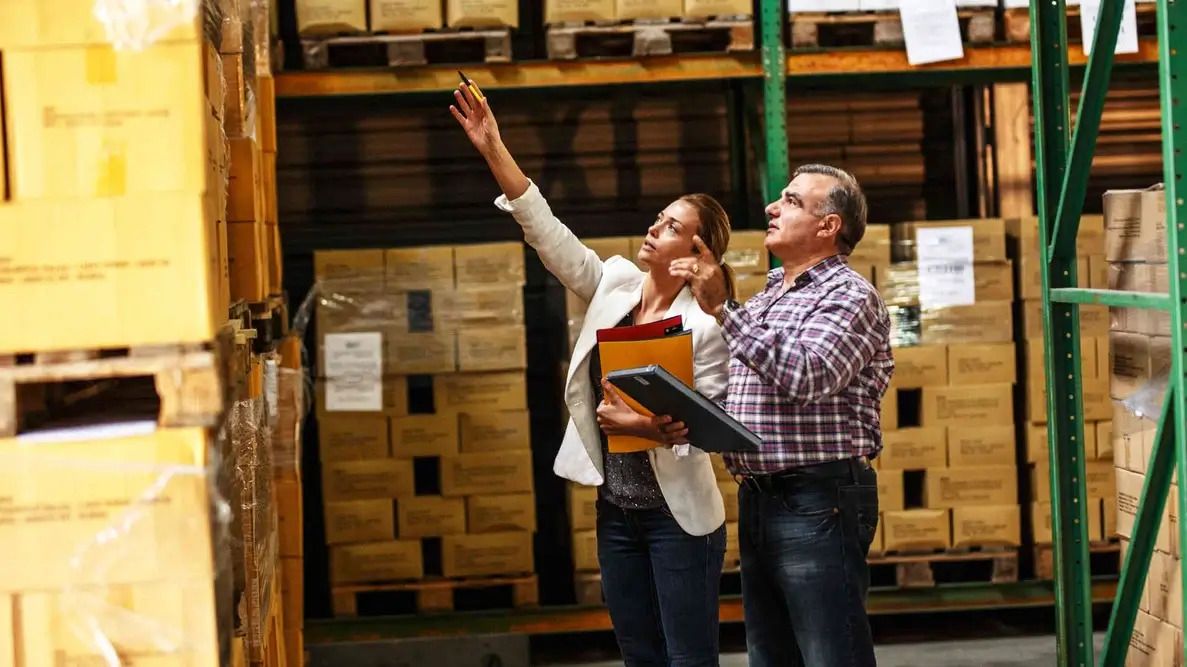
7. Lack of Employee Training
Employees who are not properly trained in inventory management may mishandle stock, mislabel products, or fail to follow proper storage procedures. These mistakes contribute to spoilage, inefficiencies, and financial losses. A lack of knowledge about food safety regulations and storage best practices can further exacerbate inventory issues, leading to non-compliance penalties.
Solution: Providing regular training on inventory systems and storage best practices enhances efficiency and minimises losses due to human error. Incentives for reducing waste can encourage employees to follow best practices consistently. Establishing clear standard operating procedures (SOPs) for inventory handling can ensure consistency and accountability across the organisation.
By addressing inefficiencies and investing in modern solutions, food suppliers can turn inventory management challenges into opportunities for cost savings and increased profitability. Implementing automation, improving forecasting, optimizing storage, strengthening supplier partnerships, and utilizing real-time monitoring systems help reduce financial losses and enhance operational efficiency.
Embracing data-driven decision-making and technological advancements is key to staying competitive. Platforms like Open Pantry provide AI-driven inventory tracking, automated stock replenishment, and predictive analytics, ensuring suppliers reduce waste, prevent stockouts, and maintain optimal inventory levels. By leveraging these tools, food suppliers can transition from reactive inventory management to a proactive, profit-driven strategy.