Wholesale Inventory Tracking: 5 Key Tips to Improve Accuracy
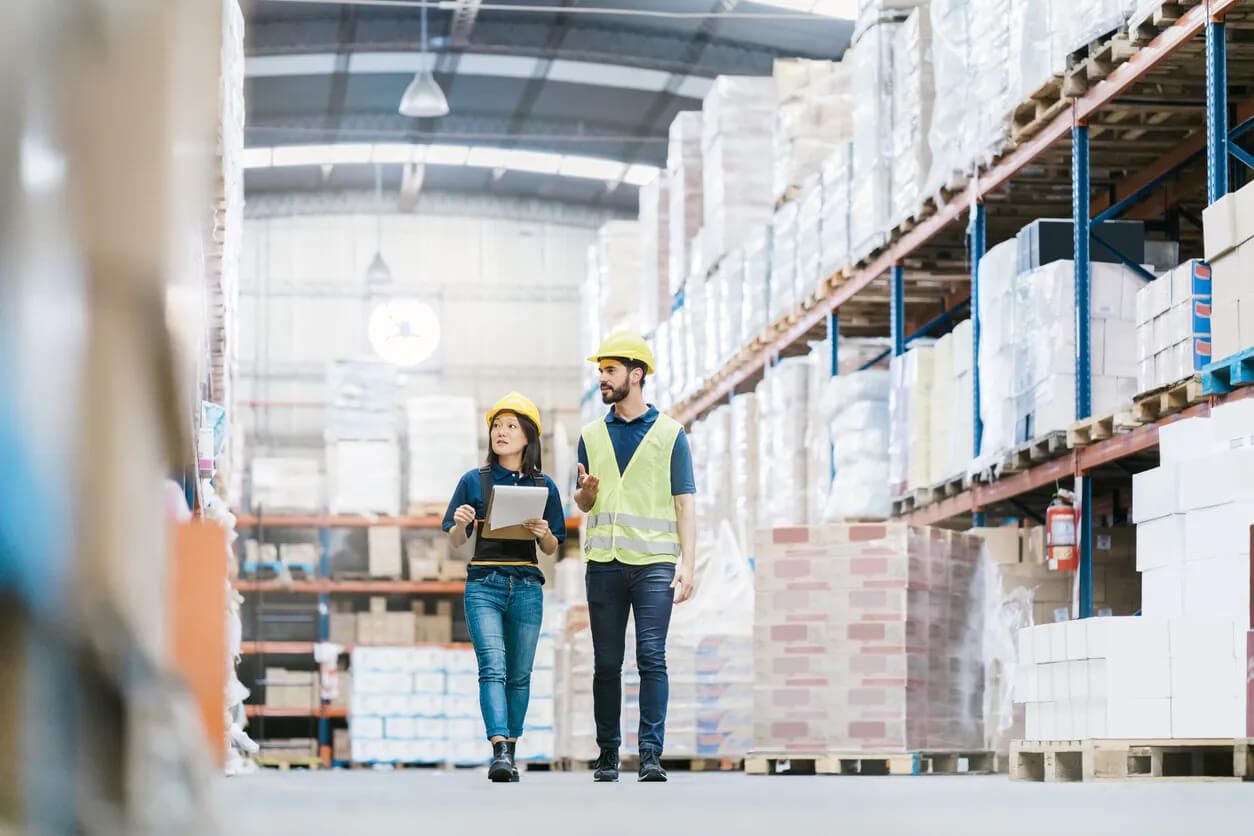
Keeping inventory accurate is very important for wholesale suppliers. If stock levels are wrong, suppliers might order too much, run out of important items, or lose money. Poor inventory tracking can also cause delays, confusion, and unhappy customers. Luckily, there are simple and effective ways to improve accuracy and make sure everything runs smoothly.
Here are five strategies that wholesale suppliers can use to track inventory better and avoid mistakes.
1. Use Barcode or QR Code Scanners for Faster and More Accurate Tracking
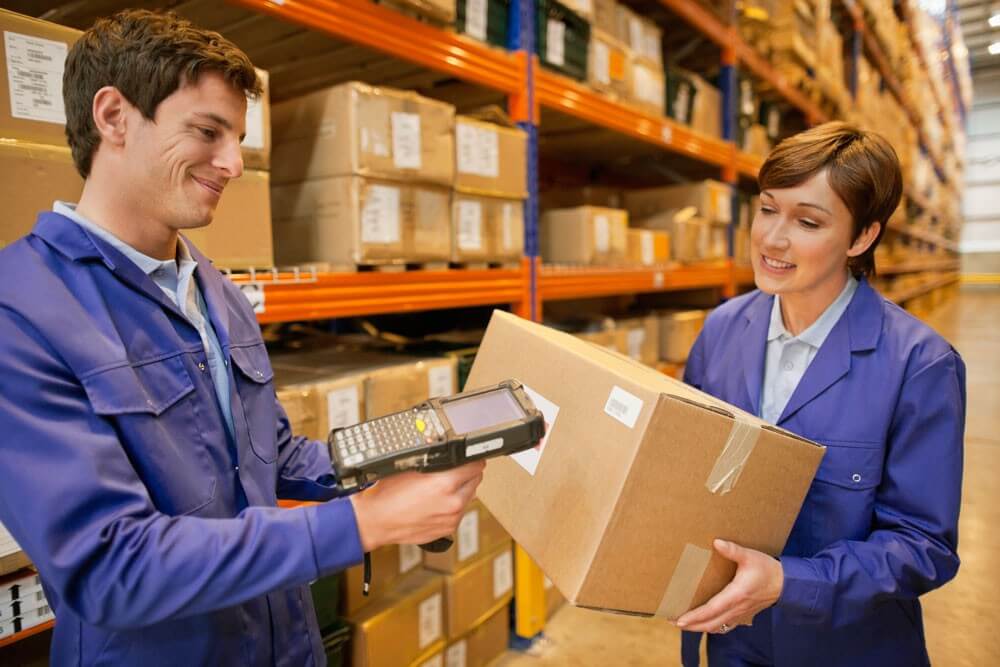
Manually counting and recording inventory is time-consuming and tends to lead to mistakes. Workers may miscount items, forget to update records, or even end up entering the wrong numbers. A better way to track inventory is using barcodes or QR code scanners. These allow workers to scan items quickly, updating stock levels instantly and reducing human errors.
For instance, a fruit and vegetable supplier receiving daily fresh produce shipments must track everything carefully. If workers count crates manually, they might enter the wrong number or forget to record a shipment entirely, leading to confusion. Without an accurate system, they could unknowingly run out of important items like tomatoes or bananas, affecting their ability to supply customers on time.
On the other hand, they might mistakenly believe they are low on certain fruits and order extra, creating excess stock that could spoil before being sold. Using a barcode or QR code scanning system removes these risks by ensuring that every crate is recorded properly the moment it arrives. This makes it easier to keep track of stock, prevents shortages or overstocking, and saves time by eliminating the need for manual counting.
2. Set Up an Automatic Reorder System to Prevent Stock Shortages
Running out of stock at the wrong time can cause major problems for wholesale suppliers. If a supplier does not keep track of inventory properly, they might not realise they are running low on important items until it is too late. An automatic reorder system solves this problem by tracking stock levels and placing orders before items run out.
For example, a wholesale bakery supplier that sells flour, sugar, and baking powder needs to ensure that these essentials are always available. If they don’t reorder on time, customers might have to wait, or the supplier could lose sales. However, with Open Pantry’s inventory system, the supplier gets automatic alerts when stock is low. The system can even reorder products automatically, making sure the bakery always has the right ingredients when needed.
Read related article Best Inventory Management Systems for Wholesale Food Suppliers
3. Use Real-Time Inventory Tracking to Keep Stock Levels Updated
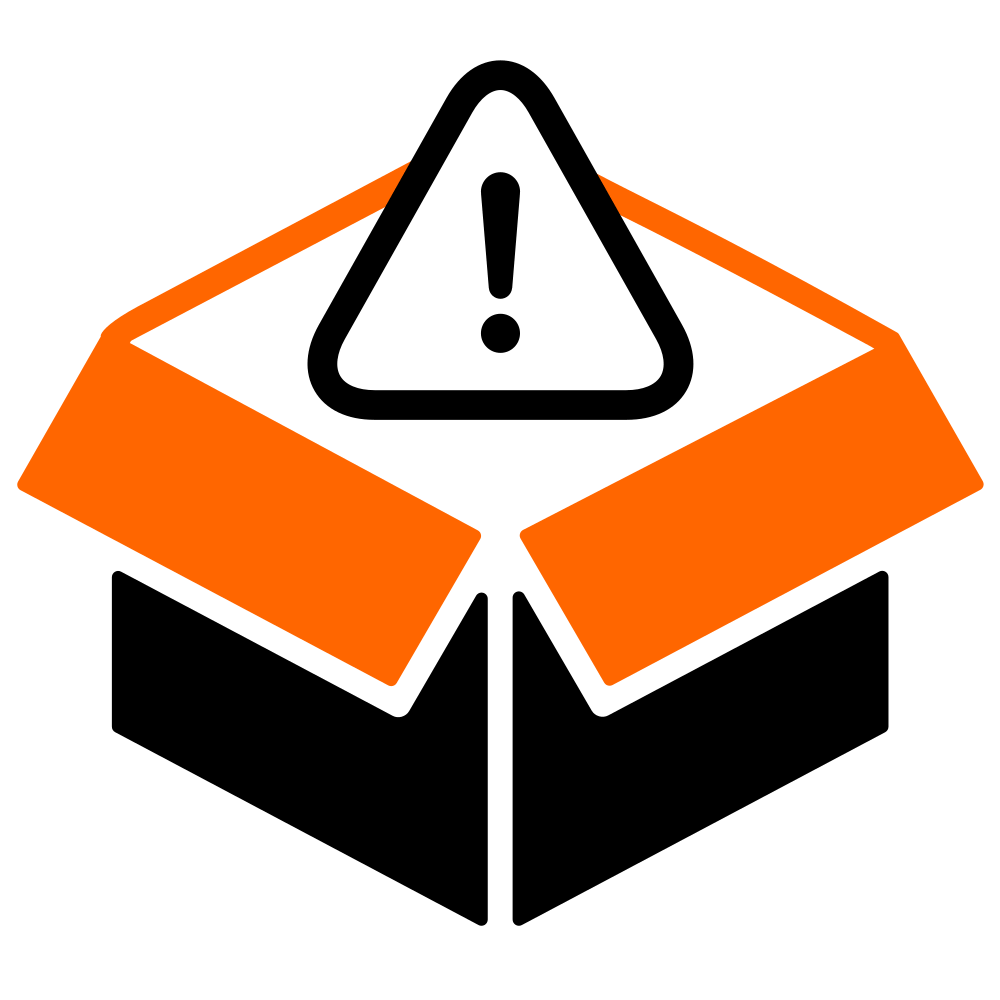
One of the biggest problems wholesale suppliers face is outdated stock information. If inventory is only updated once a day or once a week, suppliers might make decisions based on incorrect numbers. Real-time inventory tracking ensures that stock levels are updated the moment a product is sold, received, or moved.
A frozen food wholesaler dealing in ice cream, frozen vegetables, and seafood relies heavily on accurate stock tracking. If they think they have more frozen shrimp than they actually do, they might delay ordering and end up running out. Open Pantry’s real-time inventory tracking system updates stock immediately, so suppliers always know exactly how much they have. This prevents overstocking, understocking, and last-minute surprises.
4. Keep the Warehouse Organised to Reduce Inventory Mistakes
A disorganised warehouse can cause big problems for wholesale suppliers. When items are not stored properly, workers may struggle to find them, leading to wasted time, incorrect stock counts, and delivery delays. Misplaced products can also create confusion, making it hard to know what is actually in stock. While labelling shelves and grouping similar items help, manual organisation is not always enough. The best way to keep inventory accurate is by using a digital warehouse management system (WMS) that tracks product locations and updates stock levels automatically.
A spice wholesale supplier dealing in black pepper, cinnamon, and turmeric needs a clear system to avoid mix-ups. If spices are stored randomly, a worker might place paprika in the cumin section by mistake, leading to errors in stock records. A digital WMS can solve this problem by assigning each product a barcode and tracking its exact location in the warehouse. Workers can simply scan items as they move them, and the system will update the inventory in real-time. This ensures products are stored correctly, prevents stock mistakes, and makes it easy to locate items quickly, thereby making warehouse operations much smoother.
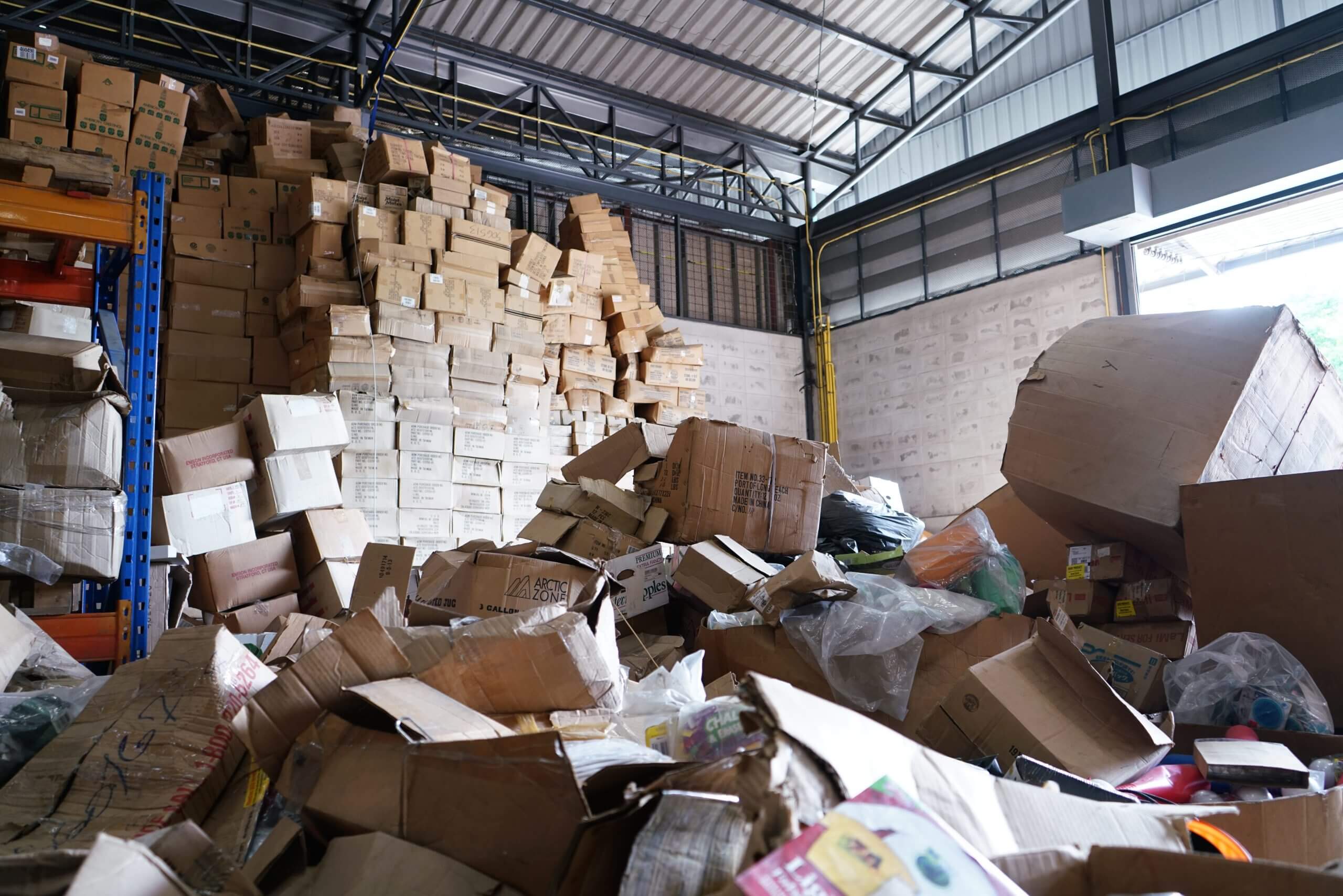
5. Conduct Regular Inventory Audits to Catch and Fix Mistakes
Even with the best technology, mistakes can still happen. Products can get misplaced, records might not match actual stock, or theft can occur. That’s why regular inventory audits are important. These checks help wholesale suppliers find errors before they turn into bigger problems.
A wheat and grain wholesale supplier stores large quantities of rice, oats, and barley. Over time, small mistakes can add up, leading to incorrect stock levels. Open Pantry’s digital inventory records make audits easier by allowing suppliers to compare system records with physical stock. This helps suppliers quickly find and fix discrepancies, keeping inventory accurate and preventing losses.
Accurate inventory tracking is essential for wholesale suppliers to avoid costly mistakes, keep customers happy, and ensure smooth operations. By using barcode scanners, setting up automatic reorder systems, tracking inventory in real-time, keeping warehouses organised, and conducting regular audits, suppliers can significantly improve their stock management. Open Pantry makes all of these processes easier by providing smart tracking systems, real-time updates, and warehouse organisation tools. With these strategies in place, wholesale suppliers can save time, reduce errors, and run their operations more efficiently.